Beverage Grade CO2: Everything You Need to Know in Bars, Breweries & Restaurants | Coldbreak
Compressed gas plays a crucial role in the service industry as it’s extensively used to dispense and carbonate beverages. Carbon dioxide is a naturally occurring gas that is colorless, odorless, and non-toxic. Additionally, beverage grade gases, such as beverage grade CO2, are subjected to specific industry standards to prevent off-flavors and impurities that could impact the final product’s taste and appearance. Food grade CO2 can even extend the shelf life of food items like pastries and salads.
What is Beverage Grade Carbon Dioxide?
There are a variety of grades of carbon dioxide, each with its own specific properties and uses. The most common grades are beverage grade, industrial grade, and medical grade. Beverage grade carbon dioxide is a type of compressed gas that meets the requirements for use in food production, and where we will focus our attention for this article. It contains significantly less impurities than what is found in normal air, making it safe to consume as an ingredient or additive.
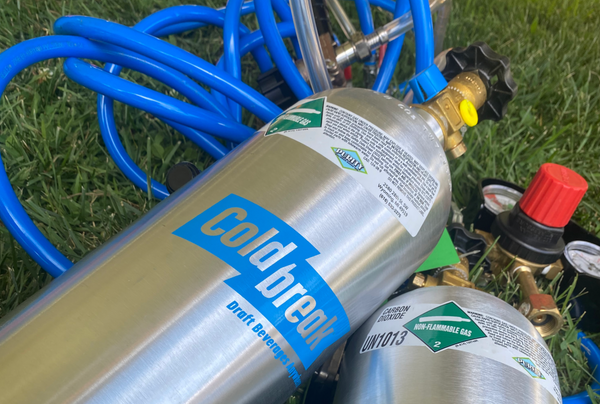
Understanding the Basics of CO2
Compression: The process begins with compressing CO2 gas. Compressors are used to increase the pressure of the gas, typically drawing it from the atmosphere. Compression is achieved by reducing the volume of the gas, resulting in a significant increase in pressure.
Filtration: To ensure the purity of the CO2, manufacturers employ filtration systems to remove any impurities or contaminants that may have been introduced during the compression process. This step helps meet the standards for food-grade carbon dioxide. This filtration process is crucial for producing CO2 that meets the high purity standards required to carbonate beverages effectively.
Cooling: After compression, the CO2 gas is cooled to facilitate condensation. Cooling allows the gas to transition from its gaseous state to a liquid state, which is essential for filling small tanks efficiently.
Liquid CO2 Storage: The condensed CO2 is stored in large tanks or cylinders as liquid CO2 until it is ready to be filled into smaller containers. These storage tanks maintain the CO2 in its liquid state under controlled conditions.
Filling Small Tanks: When filling small tanks, manufacturers use specialized equipment such as filling stations or filling manifolds. The liquid CO2 is carefully transferred from the storage tanks to the small tanks under controlled pressure and flow rates.
Quality Control: Throughout the entire process, manufacturers implement rigorous quality control measures. This includes testing the purity of the CO2, ensuring proper pressure levels, and conducting safety inspections to verify the integrity of the small tanks. Most small tanks are certified for 5 years and their date is permanently stamped onto the tank. Once the date has passed, tanks must be re-certified before a manufacturer can re-fill the tanks (typically a $10-$20 fee).
Portable Tanks: 5 and 10 Pound
Bars, breweries, and restaurants often utilize 5 and 10 pound cylinders to store and transport compressed CO2. It is advisable to keep an extra tank on hand to ensure an uninterrupted supply. Using high-purity gas cylinders for beverage applications is crucial to ensure no harmful impurities affect the taste of the beverages. These smaller tanks are easily maneuverable, allowing for effortless exchanges, refills, and replacements.
Small CO2 tanks can be divided into two types: aluminum and steel cylinders. Each type has its own set of advantages and considerations.
Aluminum tanks are made from high-strength aluminum alloy, providing durability and a sleek appearance. They are lightweight, making them easy to handle and transport, and offer excellent corrosion resistance. However, aluminum tanks can be more expensive upfront, have a lower pressure rating, and are more susceptible to physical damage.
On the other hand, steel tanks are constructed from high-quality steel with protective coatings to prevent corrosion. They are known for their durability, affordability, and higher pressure rating. However, steel tanks are heavier, making them more challenging to handle and transport, and they are more susceptible to rust and corrosion if the protective coating is compromised.
Safety
As a business owner dealing with CO2 in our daily operations, safety is paramount when handling this essential yet potentially hazardous gas. Ensuring the safe handling of CO2 is particularly important when it is used to carbonate beverages, as any contamination can affect the quality and safety of the final product. Here’s how we approach CO2 safety in our business:
Understanding CO2 Risks: CO2 is colorless and odorless, making it hard to detect. In high concentrations, it can displace oxygen, leading to asphyxiation. We’re always mindful of this, especially in confined spaces.
Proper Training and Awareness: Everyone on our team receives training on CO2’s properties and potential hazards. This knowledge is crucial for safe handling and quick response in case of emergencies.
Use of Protective Gear: When handling CO2 cylinders, we always wear protective gear, including gloves and safety goggles. This is non-negotiable, as it protects us from the high pressure of the gas.
Responding to CO2 Leaks:
Ventilation: The first step in case of a leak is ensuring adequate ventilation. We open doors and windows to disperse the gas. Proper ventilation is crucial to prevent any contamination of CO2 used to carbonate beverages, ensuring the final product remains safe and of high quality.
Shutting Off the Source: If it’s safe to do so, we immediately shut off the CO2 source to stop the leak.
Evacuation and Emergency Services: If a large leak is detected, we evacuate the area and call for emergency services. Their expertise is critical in safely resolving the situation.
CO2 Detectors: Our business is equipped with CO2 detectors to alert us to any dangerous levels of gas.
Regular Equipment Checks: We regularly inspect and maintain our CO2 storage and dispensing systems. This proactive approach helps prevent leaks and ensures the systems are functioning correctly.

Tank Certification
The certification of CO2 cylinders is a critical aspect of managing food grade CO2, particularly in ensuring safety and compliance with industry standards. This process involves a series of inspections and tests to ascertain the integrity and safety of the cylinders used to store and transport CO2. Certification ensures that the CO2 tanks used to carbonate beverages meet the required safety and purity standards. The primary goal of cylinder certification is to prevent accidents stemming from cylinder malfunction, which can lead to CO2 leaks, ruptures, or other hazardous situations.
Cylinder certification typically follows a strict schedule, with most jurisdictions mandating an inspection every five years. During these inspections, the cylinders undergo several tests, including visual examinations, pressure tests, and checks for any signs of wear, corrosion, or damage. The visual inspection is crucial, as it can detect issues like dents, cracks, or rust, which may compromise the cylinder’s integrity. Pressure testing, often involving hydrostatic methods, assesses the cylinder’s ability to safely hold CO2 under operational pressures. This test ensures that the cylinder material retains its strength and elasticity under pressure without leaking or bursting.
Furthermore, the certification process also includes verifying the cylinder’s compliance with current regulations and standards. This includes checking the cylinder’s markings, which indicate the manufacturer, date of manufacture, and the last test date. These markings are essential for tracking the cylinder’s history and ensuring that it is not used beyond its safe operational lifespan.
After passing these inspections, the cylinders are stamped or labeled with a new certification date, indicating their compliance and safety for continued use. If a cylinder fails any part of these inspections, it must be repaired, retested, or decommissioned, depending on the severity of the issue.
Shipping CO2 Tanks: Ordering Equipment Online
CO2 is classified as a hazardous material due to its high pressure and potential to asphyxiate in high concentrations. This classification means that there are stringent rules around packaging, labeling, and documentation when shipping CO2 tanks. Most carriers require that CO2 tanks be shipped empty or with minimal pressure to reduce the risk of explosion or leakage.
Proper shipping practices are essential to maintain the integrity of CO2 used to carbonate beverages, preventing any contamination or safety hazards.
Before shipping a CO2 tank, it’s important to check with the specific carrier regarding their policies on hazardous materials. Carriers such as UPS, FedEx, and USPS have detailed guidelines and restrictions for shipping hazardous materials, including pressurized gases. You’ll need to ensure that the tank is properly labeled with the appropriate hazardous material labels and that all required documentation is completed and attached.
Federal regulations in the United States prohibit the shipment of full CO2 tanks that exceed a certain size, due to the risks associated with transporting pressurized gases. The specific limitation is on tanks that are larger than 2.2 pounds (1 kg) water capacity. This restriction is in place to mitigate the dangers posed by the transportation of larger quantities of compressed gas, which can include risks of explosion, leakage, or other hazardous incidents in transit.
The 2.2 pounds water capacity limit essentially means that smaller CO2 cartridges, typically used in soda makers, beer keg systems, and other small-scale applications, can be shipped under certain conditions, following proper safety protocols and regulations. However, larger tanks, which are commonly used in commercial settings or for larger scale operations, fall under different transportation guidelines and are generally not allowed to be shipped when full.
74 gram Cartridges
Leland Limited, Inc (US Agent) has a special permit for DOT 39 cylinders, authorizing the transportation of their cartridges via motor vehicle, rail freight, cargo vessel, and cargo aircraft only:
-
As long as they are in the original packaging.
-
Maximum cartridge fill to 75%
-
Must be packaged with outer packaging, for shipments.
-
A copy of the special permit must accompany the shipment in any vessel or aircraft.
Ensuring the safe transportation of CO2 cartridges is crucial for maintaining the quality of CO2 used to carbonate beverages.
Carbon Dioxide Hazmat Classification
-
UN 1303 (Carbon Dioxide)
-
Hazard class 2.2 (NON–FLAMMABLE COMPRESSED GAS)
-
Packaging Group: n/a
Understanding the hazmat classification of CO2 is essential for safely handling the gas used to carbonate beverages.

CO2 Supply and Quality
Ensuring a reliable and high-quality CO2 supply is crucial for businesses in the food and beverage industry. The quality of CO2 can significantly impact the taste, texture, and overall quality of carbonated beverages. To assess supply risk, it’s essential to understand the source of the CO2, the production process, and the quality management practices in place.
When selecting a gas supplier, look for a reputable company that adheres to required purity specifications and has a robust quality management system. This ensures that the CO2 you receive is free from impurities that could affect your beverages. Additionally, consider the type of CO2 cylinders used, such as steel cylinders, which are known for their durability and ability to withstand high pressures.
Regular testing and analysis of the CO2 supply are vital to identify any impurities or contaminants that may affect the quality of the final product. Partnering with an independent ISO-certified lab can provide an extra layer of assurance, ensuring that your CO2 supply consistently meets industry standards. This proactive approach helps maintain the high quality of your carbonated beverages and supports the overall success of your business.
Best Practices for CO2 Use
To ensure the safe and efficient use of CO2 in your establishment, follow these best practices:
-
Proper Handling and Storage: Handle CO2 cylinders with care, and store them in a well-ventilated area away from heat sources and flammable materials. This minimizes the risk of accidents and ensures the safety of your staff and customers. Proper handling and storage of CO2 are crucial for maintaining the quality of CO2 used to carbonate beverages.
-
Regular Maintenance: Regularly inspect and maintain your dispensing systems. This includes cleaning and replacing worn-out parts to prevent malfunctions and ensure consistent performance.
-
Proper Installation: Ensure that CO2 systems are installed correctly, with all connections secure and leak-free. Proper installation is crucial for the safe and efficient operation of your CO2 systems.
-
Training and Education: Provide comprehensive training and education to your staff on the safe handling and use of CO2. This includes emergency procedures in case of a leak or other incident, ensuring that everyone knows how to respond appropriately.
-
Quality Control: Regularly test and analyze your CO2 supply to ensure it meets required purity specifications. This helps maintain the quality of your carbonated beverages and ensures compliance with industry standards.
By following these best practices, businesses can ensure a safe and efficient CO2 supply chain, providing high-quality carbonated beverages to their customers.
Troubleshooting and Maintenance
Common issues with CO2 systems include leaks, contamination, and equipment failure. To troubleshoot and maintain your CO2 systems effectively, follow these steps:
-
Identify the Problem: Determine the source of the issue, whether it’s a leak, contamination, or equipment failure. Accurate identification is the first step in resolving the problem.
-
Shut Down the System: Immediately shut down the CO2 system to prevent further damage or contamination. This is crucial for safety and to prevent the issue from escalating.
-
Inspect and Clean: Conduct a thorough inspection of the system and clean any affected areas to prevent contamination. This helps maintain the integrity of your CO2 supply.
-
Replace Worn-Out Parts: Replace any worn-out or damaged parts to ensure the system is functioning properly. Regular maintenance and timely replacements are key to preventing system failures.
-
Test and Analyze: After addressing the issue, test and analyze the CO2 supply to ensure it meets required purity specifications. This step is essential to confirm that the problem has been resolved and that your CO2 supply is safe and of high quality.
Regular maintenance and troubleshooting can help prevent issues with CO2 systems, ensuring a reliable and high-quality CO2 supply. Regular maintenance and troubleshooting are essential for ensuring the CO2 used to carbonate beverages remains free from impurities. By staying proactive, businesses can maintain the efficiency and safety of their CO2 systems, supporting the consistent delivery of high-quality carbonated beverages.
Where to Purchase CO2?
Gas Supplier Companies: Companies that supply industrial gases (like oxygen, nitrogen, helium, and carbon dioxide) usually have the capability to refill CO2 tanks. Most have delivery vehicles that make rounds in the city, exchanging tanks at businesses that use a lot of it. Your local gas supplier should be the first place you look for filling tanks.
Homebrew Supply Shops: If you're into homebrewing, local homebrew shops are a great place to check. They frequently offer CO2 tank exchanges, as CO2 is used in carbonating beer. Pro tip: Check the certification date stamped on the tank before swapping and find one that is close to the one on your tank. You'll have to re-certify it every 5 years to make sure its safe to use.
Fire Extinguisher Service Companies: Companies that service fire extinguishers often have the facilities to refill CO2 tanks, since carbon dioxide is a common content in certain types of fire extinguishers.
Welding Supply Stores: These stores typically have the equipment and capability to refill CO2 tanks, as carbon dioxide is commonly used in welding processes. If going this route, make sure they have the capabilities to fill your tank with food grade gas.
Paintball Equipment Stores: Carbon dioxide is widely used in paintball guns, so stores specializing in paintball equipment often provide CO2 refilling services. Again, if going this route, make sure they have the capabilities to fill your tank with food grade gas.
Beverage Supply Companies: Suppliers of soda and beer dispensing equipment often deal with CO2 tanks and may offer refilling services.
Hydroponics Stores: Carbon dioxide is used in hydroponics to enhance plant growth, so stores specializing in hydroponics supplies might offer CO2 refills or exchanges.
Summarizing the Core Insights
Food grade carbon dioxide in bars, breweries, and restaurants plays a pivotal role. Its applications range from carbonating beverages to extending the shelf life of various food products. The stringent processes involved in producing, storing, and distributing this gas ensure its purity and suitability for consumption. With options for refilling and exchanging tanks ranging from specialized gas supply companies to local homebrew shops, fire extinguisher service companies, and even hydroponics stores, businesses in the food and beverage industry have diverse and accessible solutions for their carbon dioxide needs. These establishments must be diligent in maintaining the quality and safety of their carbon dioxide supplies, always ensuring that their tanks are properly certified and handled. Whether opting for lightweight aluminum tanks or the sturdier steel alternatives, the importance of selecting the right type of tank to meet specific operational demands is equally crucial. This careful balance of quality control, safety standards, and practicality in the use of food grade carbon dioxide is essential for the seamless operation and success of businesses in this dynamic industry.